DICV Inaugurates Advanced Mechatronics Lab
DICV has launched a new Mechatronics Lab, enhanced software verification efficiency and cutting costs by up to 80%.
745 views | Date: August 19, 2024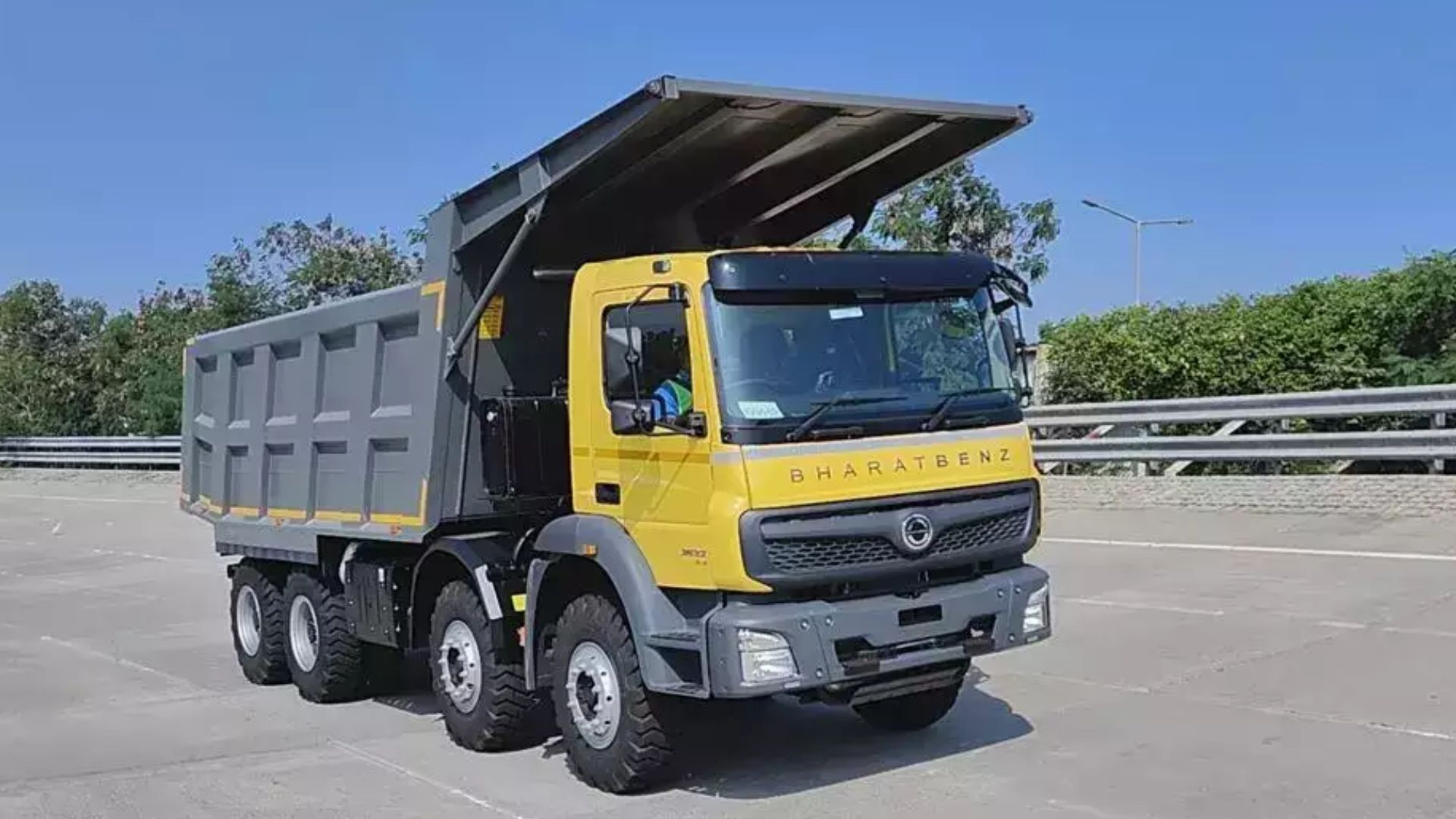
Chennai- Daimler India Commercial Vehicles (DICV)., a subsidiary of Daimler Truck AG., has launched a state-of-the-art Mechatronics Lab at its Oragadam facility. The lab enhances software architecture verification and validation, delivering cost efficiencies of 70-80% compared to traditional methods. Using agile methodologies, it speeds up bug identification and resolution, reducing testing and verification times from weeks or months to just days.
DICV’s Mechatronics Lab verifies and validates software feature functionality for trucks and buses that not only meet current safety standards, but also helps Daimler Truck products manufactured in DICV stay ahead of the curve in meeting future global safety regulations.
Mr. Pradeep Kumar Thimmaiyan, President of Product Engineering & Chief Technology Officer at Daimler India Commercial Vehicles, said, “Our new Mechatronics Lab signals a transformative phase in our Research and Development operations, ushering us into an era that underscores enhanced agility and breakthrough innovations. Beyond validation, our Mechatronics Lab stands as a hub for innovation, positioning us uniquely on the global stage. Already, the lab is the core of our future electrical and electronic architectures. The DICV Mechatronics Lab complements the company's long-term vision, positioning it at the forefront of technological advancements in the commercial vehicle sector. It underscores our commitment to 'Make and Develop in India, for India and the World’, embodying our vision to not only cater to domestic needs but also to set new benchmarks internationally.”
Mr. Dilip Shrivastava, Head of Mechatronics and Software Technology, Daimler India Commercial Vehicles said, “Our Lab can verify and validate around 300 features, encompassing over a thousand signals within 10 days, and can verify 600 fault codes in a developing product in just a few weeks, which otherwise would have taken months. Our aim is to ensure our software architecture gets verified and validated before it gets embedded in our trucks and buses as early identification of software bugs which saves enormous developmental cost. Keeping our long-term vision in mind we are bringing such efficiencies that can accelerate product development cycles for which our Mechatronics Lab will play a lead role. By establishing the lab, evaluation of diverse vehicle architectures has become seamless, eliminating the need for multiple test vehicles while enhancing the overall efficiency.”
DICV's new Mechatronics Lab will play a key role in advancing R&D by improving the efficiency, safety, and performance of its trucks and buses. It accelerates the development of new vehicle generations by enabling the simulation of rare fault cases, ensuring thorough verification and validation. The lab includes a flashing station for pre-production ECU checks, reducing errors and re-releases, and an ADAS setup that replicates on-road data for software adjustments, cutting costs and vehicle dependency. Additionally, it allows safe Driver State Monitoring (DSM) verification without risky in-vehicle trials.
Over the past decade, DICV has set benchmarks for safety and efficiency in the commercial vehicle industry, known for its industry-leading total cost of ownership. The new Mechatronics Lab will further this legacy, introducing advanced safety features like AEBS, Blind Spot Assist, Driver Drowsiness Alert, and Lane Departure Warning. DICV remains dedicated to delivering vehicles that excel in safety, efficiency, and value, ensuring continued success for its customers.
Leave a Response
You must be logged in to respond.
Responses
No responses yet. Be the first!